The future is circular
Phosphorus, iron, and rare earths — the Federal Institute for Materials Research and Testing (BAM) is investigating how important materials can be preserved and reused
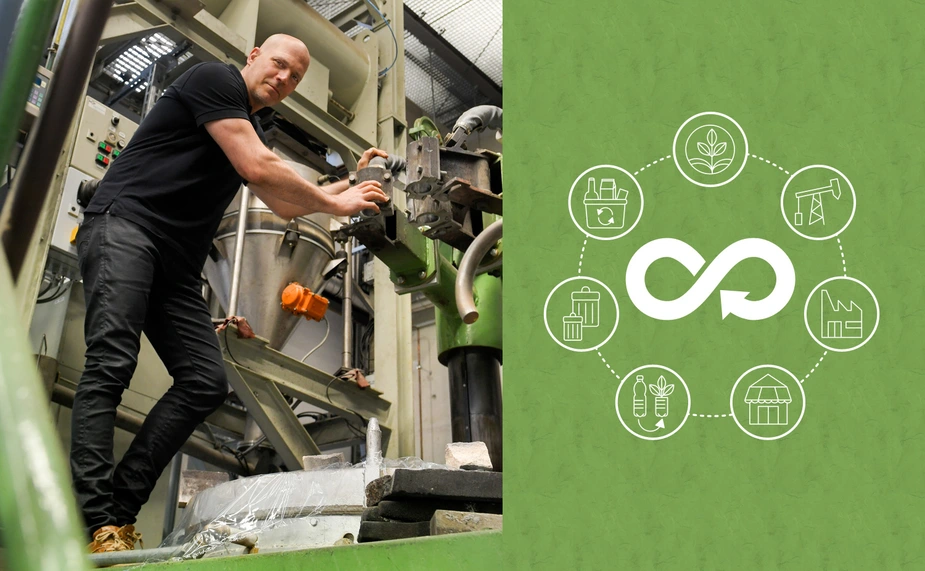
Talking to Christian Adam, an air of the eternal lies in the room. Our conversation is about continuous cycles that recovers materials and saves resources. Sparing the environment is one important goal of the circular economy, which the head of the division “Thermochemical Residues Treatment and Resource Recovery” and his team is researching and making a reality. Prolonging the service life of products, recycling, and reproducing them saves resources and reduces waste.
This starts as early as product design. “We take into account a product’s maintenance, reuse, and recycling, and the raw materials it contains from the onset,” says Adam, who wrote his PhD thesis in process engineering after studying environmental science and technology at Berlin’s Technical University. He has been working at BAM since 2004, became a division head in 2012.
Made up of chemists, engineers, mineralogists, and geoscientists, his team is conducting in-depth research on the recycling of phosphorus. This important nutrient is absorbed by plants and must be frequently given back to the soil to enable further growth. A large chunk of the phosphorus ingested with food ends up in wastewater through human excrements, accumulating in the sewage sludge. Since sludge also contains harmful substances, it is not returned directly to the fields but typically incinerated.
Adam’s team is involved in various, international research endeavours, investigating suitable thermochemical procedures. Their goal is to make recovered phosphorus from sewage sludge ashes available to plants, while removing cadmium and lead, which are harmful for the environment.
The production of iron and steel also creates waste that could be worth reusing. In addition to recyclable amounts of iron and carbon, filter dusts and blast furnace gas also contains up to 30 percent of zinc, which is bad for production and hence ends up in landfill. Together with partners from the industry, BAM has now developed a procedure capable of removing zinc from the waste product as well as recovering iron and carbon and recycling it for use in the production of steel.
Much smaller but also much more expensive are the amounts of Scandium that are mined worldwide: about 35 tonnes annually. This transition metal, present in most rare earth deposits, is used in aluminium alloys, which are a sought-after light-weight material used in aviation. However, right now, scandium is in high demand for producing solid oxide fuel cells. Europe does not have a production facility for scandium, which is one of the most expensive elements on the world market. In cooperation with 18 partners from ten European counties, BAM is part of an EU project that investigates how scandium can be recovered from industrial materials.
“To this purpose, we are focusing on red mud, a by-product of aluminium oxide production, as well as waste from titanium dioxide production,” says Adam. Characterising the mineralogical and chemical properties of red mud and other waste substances containing scandium is another bullet point on the BAM researchers’ to-do list. This work goes towards identifying additional scandium sources. More reuse, less waste—a further step in expanding the circle economy.
By Paul Janositz for Adlershof Journal